Induction Brazing Designed for Efficiency
During the manufacturing process, the continuous flow of parts, products and joints is just as important as the integrity of the final component. For expedient, consistency and quality control, RMS offers induction brazing.
Before any induction brazing recommendations are prescribed, RMS assesses the parts and process requirements. Based on the ISO guidelines of the metal parts, we recommend the most conducive induction heating application to withstand long-term requirements.
RMS brazing experts will determine an optimal induction heating approach – that’s not only cost-effective but also, designed to match your materials brazing needs. Our induction brazing services are ideal for efficiency as well as a non-contact source of isolated heat.
With more than five decades of brazing expertise, we can help:
Maximize part quality
Minimize cycle time
Reduce production costs while developing a lean manufacturing process
Exceed the highest manufacturing standards with our induction brazing applications.
Induction Brazing Facts |
Induction brazing minimizes unwanted part distortion and annealing.
Induction heating is effective for brazing a joint quickly at the right temperature.
|
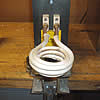 |
|
|
Our Induction Brazing process: |
1 |
The part is assembled, fluxed, brazed material positioned and then the part is positioned in an induction coil and heated until the exact temperature is reached. |
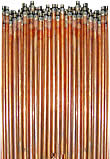 |
2 |
Next, the part is soaked at the correct temperature for proper braze flow. |
3 |
The brazed part is cooled down until it reaches room temperature, it is then washed and inspected. |
|
|
|